Digitalisierung in der Instandhaltung - Brücke zwischen den Netzwerk-Welten
04.08.2023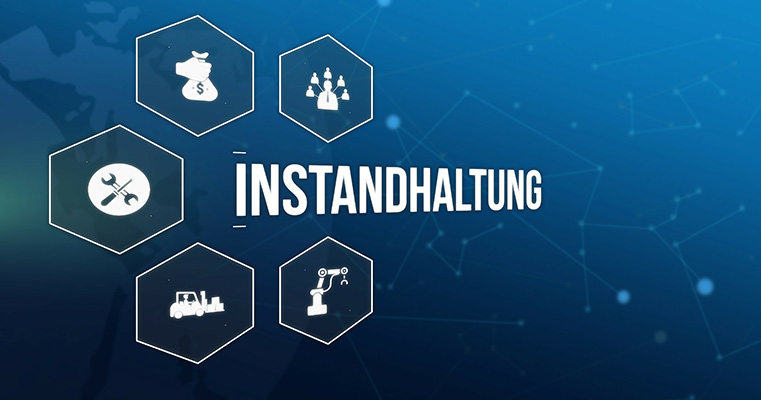
Effizienzsteigerung ist seit jeher eine der wesentlichen Antriebsfedern automatisierter Produktion. In der Vergangenheit wurden hier viele “low hanging fruits” geerntet. Gerade effizientere Produktion spielte dabei eine entscheidende Rolle. Damit ist der “Effizienz-Baum” aber noch längst nicht leer. Wenn man bedenkt, dass über ein Drittel der Kosten für die Instandhaltung der in der Anlage verbauten Assets anfallen, wird deutlich, dass es hier durchaus noch Optimierungspotenzial einzufahren gibt.
Die entscheidende Frage ist jedoch: Wie werden die für die Instandhaltung relevanten Daten erfasst und wie kommen sie aus der Feldebene in die Leitebene? PROFINET als Kommunikationsbus schafft dafür prinzipiell gute Möglichkeiten. In der Praxis wird das aber noch längst nicht konsequent genutzt. Die Gründe dafür sind vielfältig.
Netzwerk als kritischer Asset
Die Aufgabe eines Instandhalters besteht in erster Linie darin, den unterbrechungsfreien Betrieb von Anlagen zu gewährleisten. Dazu muss er kritische Assets im Blick haben und sie bei Bedarf oder bei Problemen austauschen. Kritische Assets sind unter anderem solche, die hohem mechanischem Verschleiß unterliegen, schwer zugänglich sind oder deren Tausch mit hohem Aufwand einhergeht. In der Vergangenheit hat sich hier der Blick geweitet; Fakt ist, dass nicht nur Komponenten wie Pumpen, Getriebe, Motoren, Lager, Dichtungen und dergleichen Verschleiß unterliegen. Auch das Kommunikationsnetzwerk selbst ist, wenn man so will, ein kritischer Asset, dessen reibungsloser Betrieb gewährleistet sein muss.
Unterschiedliche Interessen
Eine Erfahrung der Instandhalter ist dabei: Je homogener ein Netzwerk, desto sicherer sein Betrieb. Daher ist es ihnen in der Regel am liebsten, wenn über das Netzwerk nur produktionsrelevante Daten übertragen werden. In diesen homogenen Netzwerken kommt es zu weniger Störungen. Oder anders gesagt: Viele Instandhalter haben die Erfahrung gemacht, dass die Übertragung von zusätzlichen Smart-Sensor-Daten beispielsweise zur Steigerung von Anlageneffizienz, zur Optimierung von Energiekosten oder Zustandsdaten verschiedener Komponenten im Produktionsnetzwerk zu Störungen führen und die zuverlässige Produktion behindern können. Zudem fürchten sie um die Netzwerksicherheit, wenn sich eine übergeordnete Ebene in „ihr“ Netzwerk einklinkt, um Daten für die Prozessoptimierung auszulesen. Hier prallen die Bedürfnisse von Instandhaltern und Management aufeinander. Während den einen in erster Linie ein ausfallsicherer Betrieb wichtig ist, wollen die anderen Prozesse optimieren und Kosten einsparen. Optimiert werden sollen heute auch Instandhaltungsprozesse, die nicht unerhebliche Kosten verursachen (Bild 1). Unnötige Kosten entstehen hier beispielsweise durch den turnusmäßigen Austausch von Komponenten – unabhängig von deren Realzustand. Effizienter und nachhaltiger wäre es, Komponenten erst möglichst kurz vor ihrem Ausfall auszutauschen. Ein weiterer Punkt, der optimiert werden könnte, ist der ineffiziente Einsatz von Personal. Das Management ist neben den reinen Prozessdaten also interessiert an Zusatzinformationen über Komponenten, Energieverbräuche, Informationen zu Lastspitzen und dergleichen. Weil Instandhaltern aber oft ihr homogenes Netzwerk wichtig war, wurden dazu in der Vergangenheit vielerorts zusätzlich zum Produktionsnetzwerk Leitungen verlegt, um Smart-Sensordaten zum Management zu bringen. In Hinblick auf Effizienz ist das ein völlig kontraproduktiver Ansatz.
Netzwerk – homogen und konvergent
Dabei ist es aus Sicht des PROFINETs eigentlich kein Widerspruch, sowohl die Prozessdaten selbst als auch Instandhaltungsdaten zu Assets oder beispielsweise Informationen zu Energieverbräuchen zu übertragen. Allerdings fehlte es aus Betreibersicht bislang an den entsprechenden Tools, mit denen sich eine sichere Vernetzung homogener Netzwerke miteinander und mit der Visualisierungsebene (SCADA) mit möglichst geringem Aufwand realisieren lässt. Bisherige Lösungen erfordern IT-Know-how, das auf OT-Ebene oft nicht im notwendigen Maße vorhanden ist. Die Netzwerkexperten von Indu-Sol haben in ihren vielzähligen Vor-Ort-Einsätzen diese Probleme gesehen bzw. das verschenkte Potenzial wahrgenommen und daher nun passende Lösungen geschaffen.
Netzwerke horizontal und vertikal verbinden
Ein Kernelement dieser Lösung sind die Digitalisierungsbridges (D*Bridge), die ab der zweiten Jahreshälfte 2023 zur Verfügung stehen (Bild 2). Dabei handelt es sich um intelligente Bridge Devices, die den Datenaustausch in einem OT-Netzwerk zwischen einzelnen Maschinen automatisiert managen und nur relevanten Datenverkehr passieren lassen (Bild 3). Die D*Bridge H schafft dabei sichere, homogene konvergente Netzwerkstrukturen zur Digitalisierung zwischen Feldbussen auf der Shopfloor-Ebene (also auf horizontaler Ebene). Die D*Bridge V sorgt dann für eine sichere (vertikale) Verbindung der homogen-konvergenten Netzwerkstrukturen zur Verarbeitung der Smart-Sensordaten aus dem Shopfloor direkt in die SCADA-Ebene. Dabei ist die Installation der D*Bridges H denkbar einfach. Nach Montage auf der Hutschiene im Schaltschrank werden sie konfigurationslos mit dem Netzwerk verbunden. Die Anbindung in vertikaler Ebene (also der D*Bridge V) ist etwas komplexer. Hier wird beispielsweise eingestellt, welche Daten die Bridge passieren dürfen oder eben nicht. In der Regel wird für solche Anbindungen aber ohnehin die hausinterne IT-Abteilung zu Rate gezogen. Alternativ helfen die Netzwerkexperten von Indu-Sol gerne bei der Anpassung und Integration ins jeweilige Netzwerk. Quasi als Firewall sorgen die Digitalisierungsbridges dann für eine sichere Verbindung homogener Netzwerke und sicheren Datenzugriff. Aus Anwendersicht schlägt die Lösung zwei Fliegen mit einer Klappe: Für den Instandhalter fühlt es sich nach wie vor an, als bliebe er bei seiner homogenen Insellösung, weil die Smart-Sensordaten an der SPS vorbei ins übergeordnete Netzwerk weitergegeben werden. Das Management andererseits hat nun Zugriff auf alle Smart Sensordaten, ohne redundant Kabel bzw. Netzwerke installieren zu müssen.
SIEDS – ein Sensor für alle Fälle
Selbstverständlich müssen physikalische Größen, die Rückschluss auf den Zustand eines Assets geben, zuerst einmal erfasst werden, ehe sie dann an die SCADA-Ebene übergeben werden können. Viele neue Assets sind heute schon mit entsprechender Sensorik ausgerüstet, die ihre eigene Zustandsüberwachung ermöglichen. Über die Indu-Sol Switches der PROmesh Serie können nun ihre Daten einfach ins vorhandene PROFINET eingespeist, an die Managementebene weitergegeben und mit der Software PROmanage überwacht werden. Gerade in Brownfieldanlagen fehlen diese Sensoren jedoch an den meisten kritischen Assets. Zu diesem Zweck hat Indu-Sol den smart industrial environment digitalization sensor (SIEDS) ins Produktprogramm aufgenommen (Bild 4). Diese Industrie-Sensoren vereinigen Sensorik, Datenverarbeitung und Netzwerkkommunikation in einem kompakten IP65-Gehäuse. Die Sensoren erfassen und verarbeiten viele unterschiedliche physikalische Größen wie z.B. Schwingungen, Akustik, Temperatur oder Druck oder Feuchtigkeit. Damit sind die SIEDS für jede Art von Condition-Monitoring-Aufgabe in der vorausschauenden Instandhaltung einsetzbar. In der Regel wird ein solcher Sensor am jeweiligen Einsatzort mittels Magneten, Verklebung oder Verschraubung fixiert. (Bild 5). Über Power over Ethernet (PoE) wird er dann mit dem nächstgelegenen Switch verbunden und sichert so eine stabile Datenkommunikation. Sollte der Switch nicht PoE-fähig sein, werden entsprechende Adapter für eine externe Stromversorgung angeboten. Durch die Messung eines breiten Spektrums an physikalischen Daten werden unterschiedlichste Rückschlüsse auf Problemursachen möglich. Es gibt Anwendungsfälle, in denen beispielsweise hauptsächlich Vibrationen gemessen werden sollen, dann aber deutlich wird, dass die Umgebungstemperatur wesentlichen Einfluss auf die Prozessstabilität hat. Ein weiterer Vorteil der multi-purpose-Sensoren besteht darin, dass sie die Lagerhaltung vereinfachen, weil lediglich ein Sensortyp für verschiedenste Einsatzfälle vorgehalten werden muss.
Instandhaltung mit Realdaten planen
Mit dem SIEDS lassen sich alle relevanten physikalischen Größen zu verschiedenen Assets erfassen und Trends beobachten. Ein entsprechendes Alarmmanagement reagiert beim Unter- oder Überschreiben vordefinierter Grenzwerte. Das schafft ideale Voraussetzungen für Instandhaltung mithilfe eines Condition Monitoring Management System (CMMS). Während diese Systeme bisher im Wesentlichen bei der Instandhaltungs-Organisation unterstützen (also Personalorganisation bei Wartungsmaßnahmen, Organisation von Dienstleistern, Kennzahlenermittlung wie OEE, Ersatzeilhaltung bzw. Ersatzteilübersicht), können nun basierend auf den Daten der SIEDS entsprechend der Realzustände von Assets automatisiert Instandhaltungsmaßnahmen angestoßen werden. Anlagenverfügbarkeit, Kostendruck und Fachkräftemangel sind Herausforderungen, mit denen Anlagenbetreiber heute zu kämpfen haben. Mit cleveren Digitalisierungslösungen kann man diesen nicht nur begegnen, sondern vielfältiges Optimierungspotenzial erschließen.
Autoren: Rogèr Costa, Abteilungsleiter Marketing bei Indu-Sol und Dipl.-Ing. (FH) Nora Crocoll, Redaktionsbüro Stutensee