Retrofit in glass wool production
With HMR Automation and Indu-Sol
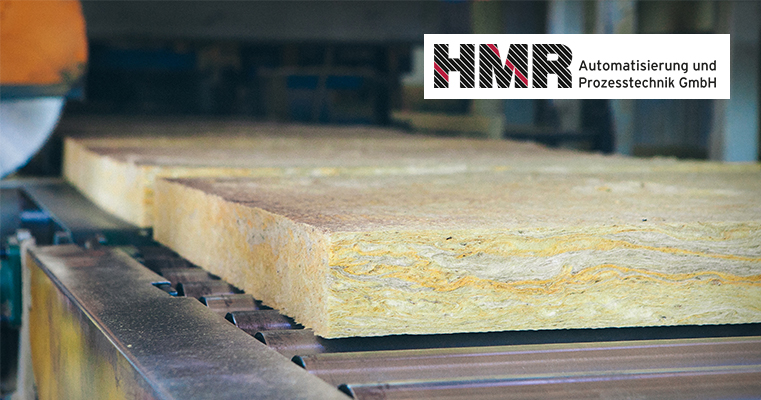
Intelligent switches are the new “watchdogs” in the network
Case study: Retrofit for fewer downtimes and better output in the production of glass wool
Automated industrial plants should produce reliable quality and be as efficient as possible. A retrofit after many years of use is therefore unavoidable in many plants. Defective components must be replaced and the machines’ mechanisms or software updated to make the plant more effective and productive once more. This also includes levelling up the performance of the communication network. If the component wear has led to production losses in the past, it makes sense to use switches with diagnostic features for the retrofit in order to better determine the causes and to be alerted in advance in the future. A large glass wool manufacturer working with HMR Automatisierung and Indu-Sol opted for this route.
HMR Automatisierung und Prozesstechnik GmbH is specialised in the implementation of automation projects in all kinds of industries, from the automotive industry to the food industry through to the production of medical equipment. Indu-Sol is a specialist in communication and network technology. At the end of 2023, both companies were involved in overhauling the communication network of an insulation manufacturer.
Working out the causes of failures
The plant’s network structure consisted of three rings. Before the retrofit, problems repeatedly occurred in the emergency off circuit. Dino Kovacic is the head of IT at HMR. Apart from providing support for the internal IT, his team is also responsible for designing and commissioning the networks for customers’ automation level. He reports: “Quite a time passes before the insulation manufacturing plant can be started up again from a standstill. No saleable goods are produced during this start-up phase, only rejects. It is therefore extremely important for the manufacturer to stabilise the production process.” ”
Dino Kovacic is the head of IT at HMR: “Before the retrofit, sporadic problems occurred repeatedly in the emergency stop communication ring. By using intelligent switches, which record the network communication to the millisecond, reliable conclusions can be drawn regarding the causes of the failures.”
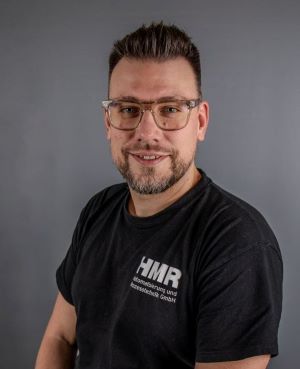
The Thuringian company, Indu-Sol GmbH, was therefore on site before the retrofit, to take measurements to determine the reasons for the failure. However, as the cause of the failure did not occur permanently, it could not be localised quickly and needed a lengthy monitoring period. The goal of the network modernisation was therefore to detect potential causes of plant failures early and to convert them into simple maintenance tasks.
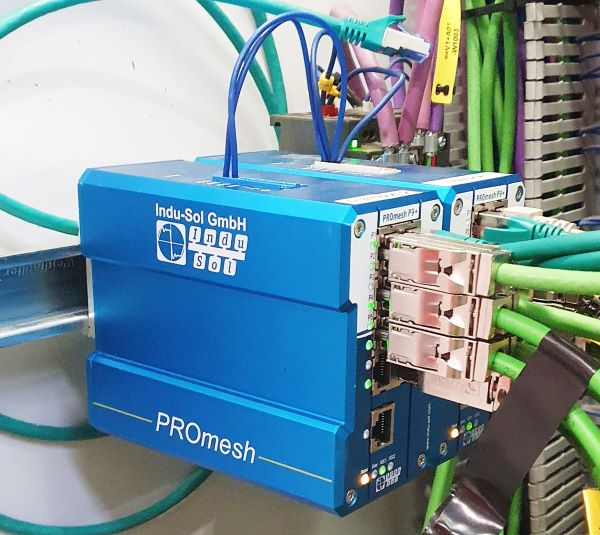
The plant operator therefore required the use of Indu-Sol’s diagnostic industrial switches. By interacting with the PROmanage maintenance analysis software, recording to the millisecond of the network communication is to be used to draw conclusions about the causes of the failure. Information, for example, about whether packet runtimes are too long, there are faults in the line, packets are lost or similar, should help to make operation of the network more stable in the future.
The PROmesh P series switches collect the network’s status data and make its physical quality, i.e. wear of the data cable, visible
Dino Kovacic has designed and implemented many networks in recent years. In the current application, he worked with Indu-Sol switches for the first time and is pleased: “In my view, the diagnostic features supplied by PROmesh switches are unrivalled on the market. Neither a leakage current or line quality measurement nor other diagnostic features offer alternative solutions.”
The PROmanage analysis software collates the data of all managed switches, visualises the causes of failures in the network so that the user can easily understand the information and alerts them in the event of anomalies. Thus, operating companies and maintenance personnel quickly know where to intervene in case of problems or where potential problems are in the offing.
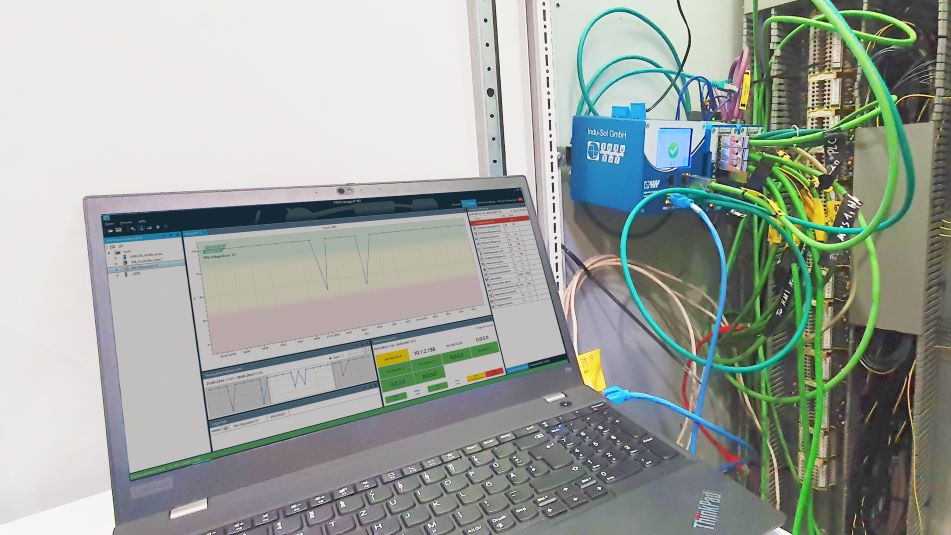
Support on an equal footing
Even before the project in the insulation production, HMR had bought measuring devices for cable certification from Indu-Sol and received more know-how in a workshop. Even then, the HMR employees found the collaboration to be very pleasant. “This all took place on an equal footing and we experienced the same again in the current project” Dino Kovacic remembers. He requested the support and advice of one of the network experts during the commissioning of the network. As it was the first time that he had used the switches, he lacked the empirical values to define thresholds. To this end, after a four-week runtime, the logs were evaluated together. The networks were also able to offer support in advance for the implementation of remote access. The OPC server used by the customer had technical challenges in retrieving the MNP files properly.
In several weeks the automation experts want to meet up with the insulation manufacturer again to analyse how well the plant is running. They will again benefit from the support of the network experts. “Together we will then take a look at the analysis software to establish whether faults still exist. It is possible that the practical production shows that we still need to optimise threshold values. We will then adjust them accordingly. And we will naturally also intervene if unscheduled faults occur”, says Dino Kovacic.
Commissioning made easy thanks to network analysis
The PROmanage® NT software used is just as important as the switches. Thanks to the intuitive usability, the automation engineers quickly got their bearings and were grateful for the clear presentation of the diagnostic data, which alternative products are unable to offer. Dino Kovacic explained: “There you can merely mirror one port onto another and then, e.g. examine the packets using the Wireshark software. However, analysing them is very complicated and is not our routine business and exceeds our competencies. We know, of course, that our colleagues at Indu-Sol can interpret this for us. But it is easier when software presents the relevant data understandably and clearly and we are able to do this work ourselves.”
The plant retrofit also benefited from the easily understandable presentation: An initial fault that could have led to a plant failure was thus found very quickly during the recommissioning. It involved a cable whose line quality was below 30 percent. The PROmesh switch identified this and the PROmanage software visualised it and issued a warning. With this information, HMR Automatisierung was then able to take a renewed measurement in the given place with a measuring device and find out that the shield of a self-configured cable was incorrectly installed. An error that was corrected quickly with the help of this information.
Does more than expected
As an external service provider, HMR has little influence on the components used in the projects. In most cases, the requirements specification stipulates which switches are to be used, or there are “release lists” of devices that can be chosen. Dino Kovacic reports: “All our in-house colleagues who have worked with the PROmesh switches to date are very impressed. In our view, the switches do even more than expected. The cost-benefit ratio is unrivalled. The products provide far more than the usual performance, but this is not reflected in the price.” He therefore recommends use of the switches, because the application has convinced him, but also because he has seen how much other customers are satisfied with them. For example, an automotive customer opts for the devices. Dino Kovacic says: “The cycle times there are extremely short and the reliability requirement is immense. This is also an argument that we cite in discussions with customers.” The certification of the switches for ethernet IP and Profinet is also advantageous. This makes their international use easier. For the future, Dino Kovacic hopes that the switches support industrial real time (IRT) and a firewall. Indu-Sol is already working on both topics. It will therefore be very interesting to see how the already very extensive product portfolio will continue to develop further in the coming years.
PROmesh switches
The PROmesh switch series products are available in different classes (product families). PROmesh P stands for managed switches with diagnostic function on the network level. They collect the network’s status data and make its physical quality, i.e. wear of the data cable, visible. If its wear reserves have been depleted too much, sporadic failures (as described in the post) occur repeatedly.
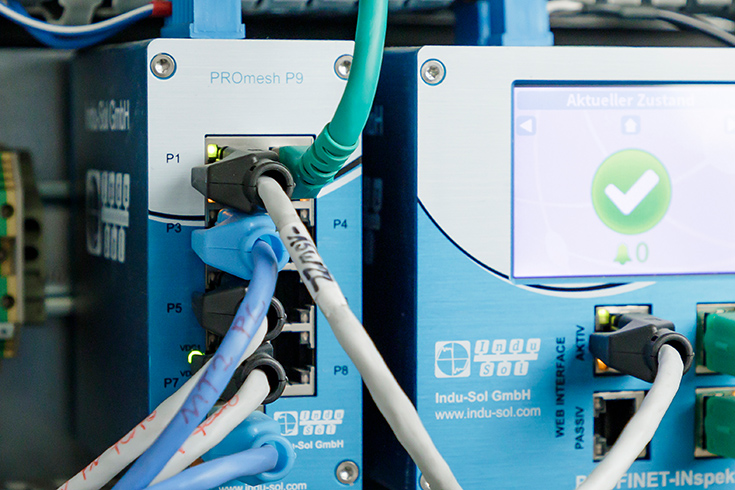
Thanks to integrated EMC monitoring, misrouted parasitic currents can be found on the shield, which otherwise often lead to failures. An overview of a few characteristics of the PROmesh P series: Online line diagnosis, leakage current monitoring, 24V and temperature monitoring, presentation of the network load with millisecond precision, diagnostic functions, PROFINET v2.4 certified, conformance class B and netload class III.
Do you have questions?
Don't hesitate to contact our expert.
Michael Röhler
Teamleader Technical Sales- +49 34491 580-186
- Send an email
Products used
About HMR Automatisierung und Prozesstechnik GmbH
HMR Automatisierung und Prozesstechnik GmbH was founded in 1982, and since then has stood for reliable and perfect implementation of automation projects. References can be found in diverse industries, from the automotive to the food industry through to medical device production. Around 100 permanent employees enable the optimum implementation of all project requirements on the highest level to the “Made in Germany” standard.
About Indu-Sol
Reliable and disruption-free communication is the guarantor for continuous production. As a manufacturer-neutral, cross-industry technology company, Indu-Sol GmbH has set itself the task of the objective assessment of quality and stability in industrial data networks. The company sees itself as an integral partner for industrial networks. Starting with network consulting/planning to the supply of components (infrastructure and diagnosis) through to support in case of failure and training the responsible personnel.
Find out more about Indu-Sol
Autoren
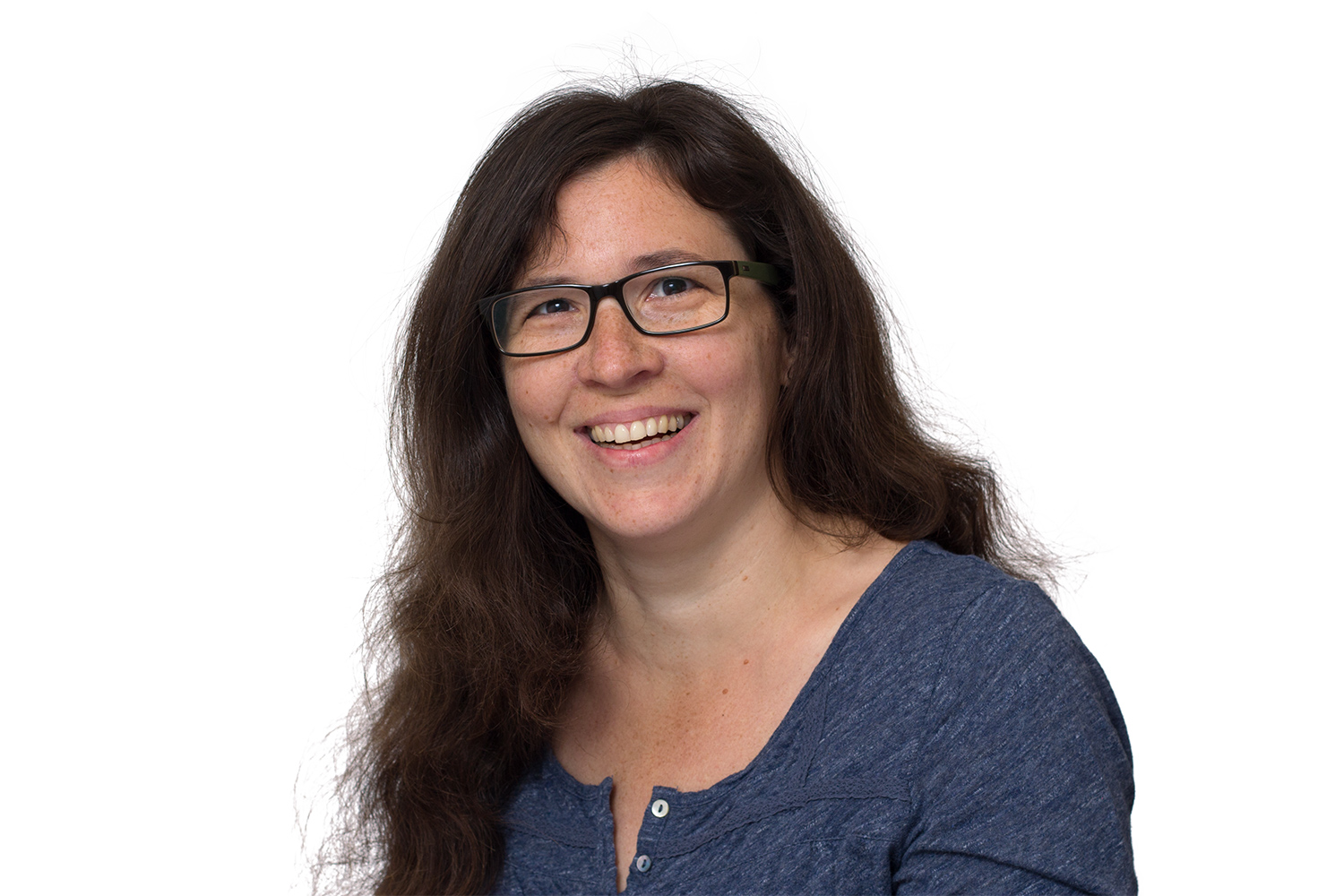