IIT - Industrial Information Technology
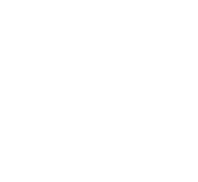
For a long time now, machine and system networks have ceased to be units that are isolated from the outside. Ethernet-based communication protocols, enabling a continuous network from sensor to cloud, are increasingly used in industrial automation. This has resulted in IT networks growing successively with networks of machines and systems (Operational Technology/OT). In addition, more and more networked devices are exchanging information, which also means an increase in total data volume.
Two main procedures have emerged as a reaction to this:
Picture on the right:
Industrial network structure Configuration example (click to enlarge)
A possible structural solution is the introduction of an intermediate level at the point where IT networks meet the networks of automation (Operational Technology/OT) – i.e. Industrial IT (IIT).
The allocation of tasks for this is as follows:
The structural concept provides for the transfer to IIT level of acyclical data traffic from applications such as printers, monitoring cameras, energy management, ERP programs, or quality assurance systems. Only the cyclical data traffic necessary for the automation processes then takes place in the OT network.
The switches of the PROmesh series are a new generation of infrastructure components that were specifically developed for the different requirements of the individual levels. The PROmesh P9, for example, has integrated earth current monitoring in addition to the data distribution and network diagnostics. Through its certification according to the highest Netload Class III, stable functioning is also ensured in the case of high data volume.
On top of all these functions, the PROmesh P20 also has an integrated router functionality, and can therefore be used in the OT and IIT environment. Regardless of which switches are used, the central network management software PROmanage® NT brings the diagnostics data of all manageable switches together on one server and displays the total network state. The individual diagnostics data remains available for up to one year. If needs be, an in-depth analysis up to the individual device is possible.
Picture on the right:
PROmesh Switches P9 and P20 with EMC-Monitoring (click to enlarge)
How does a switch work? How does it help the network operator to achieve optimal performance, and if necessary, quick and precise diagnostics? You can find out in the video The SWITCH - The Network Expert | Technology made easy: Watch now on YouTube or in the right column.
From the component to the system solution - our IIT portfolio in one brochure!
In the knowledge database, we answer the most frequently asked questions about our hardware and software.
In the knowledge database, we answer the most frequently asked questions about our hardware and software.
In the knowledge database, we answer the most frequently asked questions about our hardware and software.
The SWITCH - The Network Expert | Technology made easy Watch the video
Stay informed! Receive the latest offers and news about industrial networks and their optimization - conveniently via e-mail.